Crystallization
Tackling the challenges of batch-produced crystalline API substances during the transition to drug products
Today, the drug product manufacturing industry faces significant challenges in crystallizing API substances using batch processes. Indeed, while seeded batch crystallized APIs are in the correct polymorphic state and production is sufficiently consistent, the produced drug substance usually needs to re-engineered towards its desired size and shape for its application. Hence, the addition of one or more additional process steps besides classic seeding, growing, filtration and drying are necessary: changes in shape and size are done with different grinding and milling techniques- wet or dry – followed by seeding steps to obtain the desired size and particle size distribution, avoiding a too large variability in between the smallest and largest crystals present in the drug product powder prior to final formulation.
Although applied consistently for nearly every produced API substance, any additional process step is very costly due to inherent losses of drug product for each different additional step. Also recycling of lost material during these steps comes at a high cost to work up this product to desired properties, if even possible.
At Secoya, we have developed a unique crystallization process that allows to reduce the total number of process steps to its bare minimum from drug substance to drug product. We bring the drug substance in solution, and we generate the final CMAs of the drug product in one single process step; followed by filtration and drying. No hustle anymore to generate correctly sized seeds, no more grinding, milling and sieving of the drug products. As a true benefit, our technology bridges completely the drug substance manufacturing with the drug production facility with the direct use of the manufactured API powder.
Controlled Crystallization process
Unlike any alternative process, the Secoya crystallization technology is based on the precise control of spontaneous nucleation through the use of millifluidic tubular reactors upon cooling and different antisolvent addition possibilities. Using such capillaries, any parameter influencing the nucleation is ideally optimized and controlled.
Secoya’s crystallization technology is unique, enabling crystallization of molecules in a single process step avoiding difficult work-up when performed with conventional batch systems.
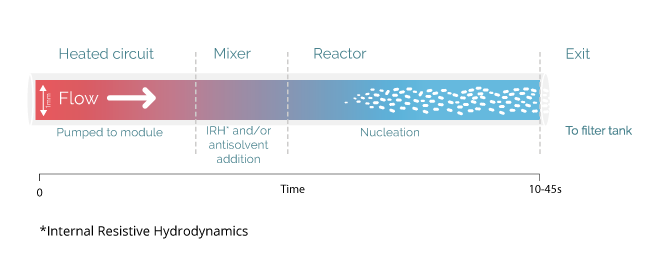
List of publications:
Nandi, S. et al., Continuous Microfluidic Antisolvent Crystallization as a Bottom-Up Solution for the Development of Long-Acting Injectable Formulations. Pharmaceutics 2024, 16, 376. https://doi.org/10.3390/ pharmaceutics16030376
Rimez et al., Cryst. Growth Des., 2018, 11, 6431-6439, https://doi.org/10.1021/acs.cgd.8b00928
Rimez et al., Cryst. Growth Des., 2018, 11, 6440-6447, https://doi.org/10.1021/acs.cgd.8b00930
Rimez et al., React. Chem. Eng., 2019, 4, 516-522, https://doi.org/10.1039/C8RE00313K
Rimez et al., J. Flow. Chem., 2019, https://doi.org/10.1007/s41981-019-00042-z
Precise control of spontaneous nucleation:
By the adaptation of reactor size to the speed of nucleation events, Secoya Crystallization Technology precisely controls spontaneous nucleation events occurring for solutes in solution. These designed reactors permit very precise changes of any important parameter to generate a stable stream of nuclei like temperature, shear rate and mixing.
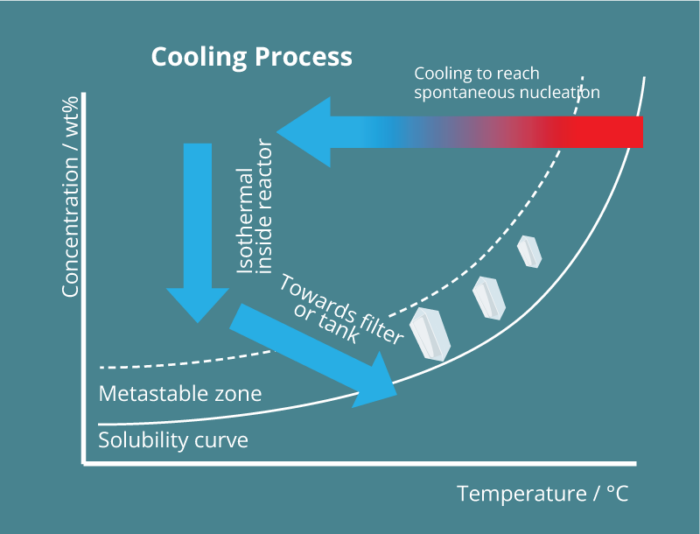
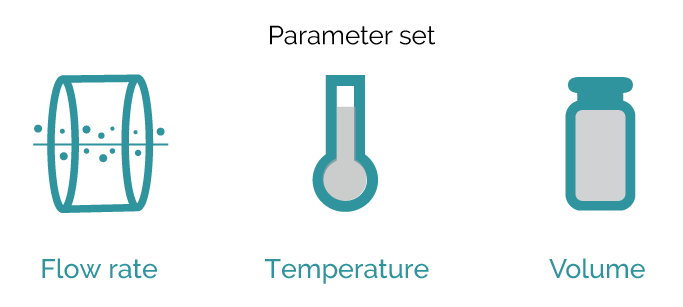
Rapid screening and development cycle
Experienced crystallization scientists will be surprised by the speed at which crystallization experiments can be conducted using the Secoya Crystallization Technology. Even more, parameter testing is further streamlined by simply inputting the desired temperatures, flow rates, and volumes, allowing the instrument to stabilize quickly. The intuitive software then facilitates swift and efficient test execution. Vast amounts of process data are generated in very short periods of time.
Versatile equipment for multiple crystallization modes
The Secoya Crystallization Technology is engineered to support various crystallization processes, including cooling crystallization, co-flow antisolvent crystallization, and frontal antisolvent crystallization. These differences enable for one single molecule different types of applications, whether as an oral dosage form, inhalation medicine, injectable, gene delivery and others.
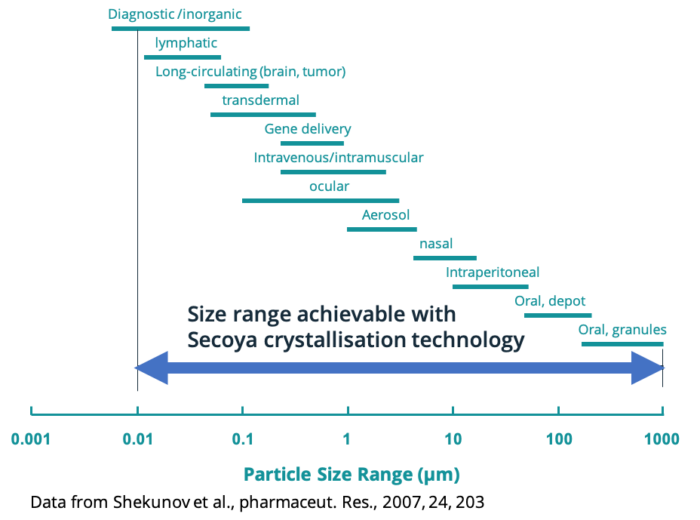
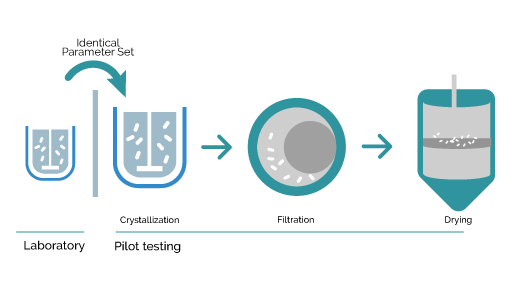
Development a complete process cycle
Once the process parameters are set at the laboratory scale, pilot unit testing can be conducted using the complete process chain from liquid state to dried product while working together with our expertise and help from industrial filtration and drying partners to enable full scale dimensioning of the final process conditions and process unit configuration.
Seamless scale-up from lab to production
The Secoya Crystallization Technology allows for a smooth transition from laboratory to manufacturing scale by maintaining the same process parameter settings in our devices, utilizing exactly identical reactor and insert combination from lab to production without any bad surprises.
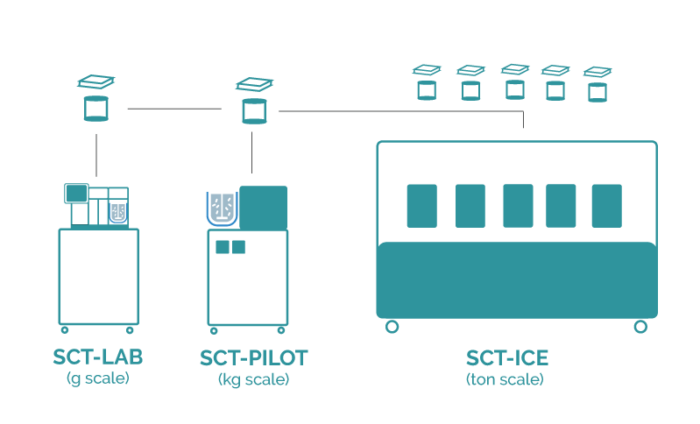
SCT user experience
Back to our Crysta’DAYS (Nove. 2023) when our partners shared their experience with our robust crystallization technology.Discover why pharmaceutical companies like Janssen or Johnson Matthey already adopted Secoya technology in-house to enhance their crystallization process for APIs.
Want to know more about the CRYSTALLIZATION TECHNOLOGY?
Want to know more about the CRYSTALLIZATION TECHNOLOGY?
![]() | Thank you for Signing Up |
